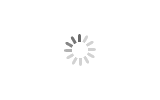
BQ series Gravity Die Casting Machine
Brand :Daseon
Product origin :China
Delivery time :30 Days
This section details two gravity die casting machines,horizontal and tiltable models,designed for precision aluminum components across industries.
Industrial manufacturers rely on gravity die casting machines to achieve high-integrity aluminum castings with minimal porosity.Our systems are engineered for automotive, aerospace, and heavy machinery applications, combining advanced process control with tooling flexibility to meet stringent production demands.
Horizontal Gravity Die Casting Machine
1.Primary Applications:The horizontal gravity die casting machine excels in high-volume production of:
--Motorcycle Systems: Wheel hubs, cylinder heads, and brake calipers.
--Hydraulic Components: Valve blocks, pump housings, and manifold castings.
--Structural Parts: Engine brackets, heat exchangers, and industrial tooling.
2.Technical Capabilities
--Process Stability: Maintains 10MPa system pressure for uniform metal filling, reducing oxide inclusions.
--Adaptive Tooling: Side cores with 120mm travel enable complex geometries, while 660–900mm adjustable formwork supports multi-cavity molds.
--Cycle Efficiency: 60mm ejection stroke minimizes part handling time, achieving cycles under 90 seconds for wheel production.
Key Specifications
Tiltable Gravity Die Casting Machine
1.Specialized Applications
Designed for thin-walled and intricate parts, the tiltable gravity die casting machine is ideal for:
--EV Components: Battery trays, motor housings, and charging port brackets.
--Aerospace Alloys: Sensor enclosures, fuel line fittings .
--Consumer Electronics: Heat sink plates, connector housings.
Technical Innovations
Dynamic Tilt Function: Offers 0–90° programmable tilt to eliminate air entrapment in critical sections.
Multi-Stage Flow Control: Adjust metal velocity via HMI to prevent turbulence in thin cavities.
Energy Optimization: Auto-idle hydraulics reduce power consumption during standby.
Key Specifications
Why Gravity Die Casting Machines Outperform Alternatives
1. Metallurgical Superiority
Ensure slower, controlled metal solidification versus high-pressure methods, reducing residual stresses in aluminum-silicon alloys.
2. Tooling Versatility
Quick-Change Systems: Switch molds in <30 minutes using standardized platens.
Side Core Integration: 120mm travel actuators produce undercuts without post-machining.
3. Sustainability Metrics
Closed-Loop Cooling: Coolant reuse reduces water consumption.
Low Emissions: Integrated fume extraction meets standards.
Gravity die casting machines demonstrate how precision engineering and adaptable controls can enhance production efficiency for aluminum components. By supporting consistent quality, minimizing material waste, and aligning with industry standards, these systems aim to address evolving manufacturing challenges while fostering sustainable growth across sectors.