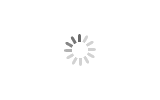
MRK200 Fully Automatic Vertical Motor Rotor Die Casting Machine
Brand :Daseon
Product origin :China
Delivery time :30 Days
The MRK200 mega-tonnage precision casting system represents the pinnacle of industrial rotor manufacturing, designed for ultra-large and high-complexity applications such as aerospace propulsion systems, marine turbine rotors, and mega-scale renewable energy components.
With a clamping force of 2,000 kN (extendable to 5,000 kN), this system combines extreme power with micro-level precision, capable of processing advanced alloys (e.g., titanium composites, nickel-based superalloys) at temperatures exceeding 1,500°C. Its adaptive multi-stage injection and AI-driven process control set new benchmarks for defect-free production in heavy-industry sectors.
Key Advantages of MRK200
1.Mega-Tonnage Clamping Force
--The mega-tonnage precision casting system delivers up to 5,000 kN of clamping pressure, ensuring mold integrity for rotors weighing over 500 kg (e.g., hydroelectric turbine blades).
--Achieves dimensional tolerances for aerospace-grade components, eliminating post-casting machining.
2.Smart Process Control
--Real-time monitoring of melt flow and thermal gradients enables dynamic adjustment of injection parameters, optimizing casting quality and reducing scrap rates.
--Advanced diagnostics predict component wear based on operational data, supporting proactive maintenance planning.
3.Extreme Material Compatibility
--Engineered for nickel-based superalloys and titanium aluminides, supporting rotors in 1,200–1,500°C environments (e.g., jet engine turbines).
--Dual-layer ceramic-coated molds extend service life under high thermal stress.
4.Energy and Resource Efficiency
--Closed-loop hydraulic systems recycle energy during idle phases, reducing power consumption versus traditional mega-tonnage machines.
--Scrap metal recycling integration cuts material waste.
MRK Series Comparison: Strategic Fit for Diverse Needs
Model | Clamping Force | Core Strength | Ideal Applications | Key Differentiator |
---|---|---|---|---|
MRK40 | 400 kN | Compact, cost-effective design | Small rotors (e.g., household appliances) | Rapid mold change, low energy use |
MRK63 | 630 kN | Vacuum-assisted precision | Medium rotors (e.g., HVAC fans) | Porosity control, multi-cavity molds |
MRK100 | 1,000 kN | High-pressure multi-stage casting | Industrial rotors (e.g., wind turbines) | Copper alloy compatibility, IoT readiness |
MRK160 | 1,600 kN | Ultra-high clamping force | Mega-scale rotors (e.g., marine engines) | Industrial IoT, extreme material compatibility |
MRK200 | 2,000–5,000 kN | Mega-tonnage precision | Aerospace, defense, and energy sectors | AI-driven control, superalloy processing |
Why Choose MRK200?
1.For Aerospace & Defense: If your production demands rotors with microstructural uniformity for extreme environments (e.g., hypersonic propulsion).
2.For Customizable Heavy Production: Fully modular design allows integration of auxiliary units (e.g., vacuum furnaces, robotic polishers) for turnkey solutions.
3.For Sustainable Mega-Scale Operations: Energy recovery and waste reduction features align with global ESG (Environmental, Social, Governance) initiatives.
Technical Specifications
The MRK200 mega-tonnage precision casting system redefines the boundaries of rotor manufacturing, offering unparalleled power, precision, and adaptability for the most demanding industrial applications. While the MRK40 to MRK160 models cater to small-to-mega-scale production, the MRK200 stands alone in its ability to merge mega-tonnage force with AI-driven intelligence, making it the ultimate choice for aerospace, defense, and cutting-edge energy sectors.
By transparently showcasing each MRK model’s unique capabilities, we empower clients to select a system that precisely aligns with their technical requirements, production scale, and sustainability goals.